Produzione
Testimonianze
Sono Andrea, ho sempre lavorato in Giardini spa e ho sperimentato i vari passaggi organizzativi e tecnologici. In particolare è stato avvincente la formazione Industria 4.0 con il totale cambiamento dell’impianto e dell’organizzazione e la possibilità oggi di lavorare con gli stessi software e sistemi su stabilimenti diversi anche distanti tra di loro.
Sono Alessandro, nell’ultimo decennio è cresciuta la formazione per lo sviluppo delle nuove tecnologie. Siamo riusciti a stare al passo con i tempi superando anche lo snodo Industria 4.0, una sfida che possiamo dire di aver vinto con la digitalizzazione dei nostri vari impianti.
Sono Luigi, provengo da un’altra azienda e ho trovato in Giardini spa la capacità di innovare continuamente e di adeguare, nei limiti del possibile, l’organizzazione alle nuove esigenze. Anche con la formazione Industria 4.0, direttamente mentre lavoravamo, abbiamo sviluppato negli anni le competenze per rispondere alle esigenze di tracciabilità, diagnostica, controllo.
Sono Moreno, ho avuto varie esperienze nel settore e nei vari impianti di Giardini Spa. Ho potuto partecipare a tutte le formazioni, inclusa Industria 4.0, e predisporre l’azienda alla sempre maggiore capacità di operare anche da remoto e in sinergia con tutte le funzioni (amministrative, logistica, trasporti ecc.).
Sono Nicola, ho svolto varie mansioni in Giardini spa e devo dire che non siamo mai stati fermi grazie anche al grosso impulso della formazione Industria 4.0 del 2019 e 2020 che oggi consente di operare digitalmente e su più impianti, sia per la produzione sia per le altre attività come la supervisione e la formulazione.
1.Da 1.0 a 4.0
L’azienda Giardini Spa opera a Castiglione del Lago PG dal 1965, nella produzione di mangimi ad uso zootecnico nelle varie forme, cubettate, in farina, in granaglie, fioccate; negli anni l’Azienda ha saputo conquistare sempre più ampie quote di mercato, sviluppando prodotti sempre più specifici per le più diverse applicazioni.
Nel corso dell’anno 2017 Giardini spa ha iniziato ad implementare, con un investimento di 2Ml.ni di euro, un progetto di profondo rinnovamento del sito produttivo e digitalizzazione integrata dei processi, seguendo in pieno le indicazioni della normativa Industria 4.0 prevista dall’articolo 1 commi da 8 a 13 della Legge 11 dicembre 2016 n°232. Con l’anno 2020 si completa la formazione di tutti gli operatori che divengono così in grado di gestire pienamente le potenzialità del sistema.
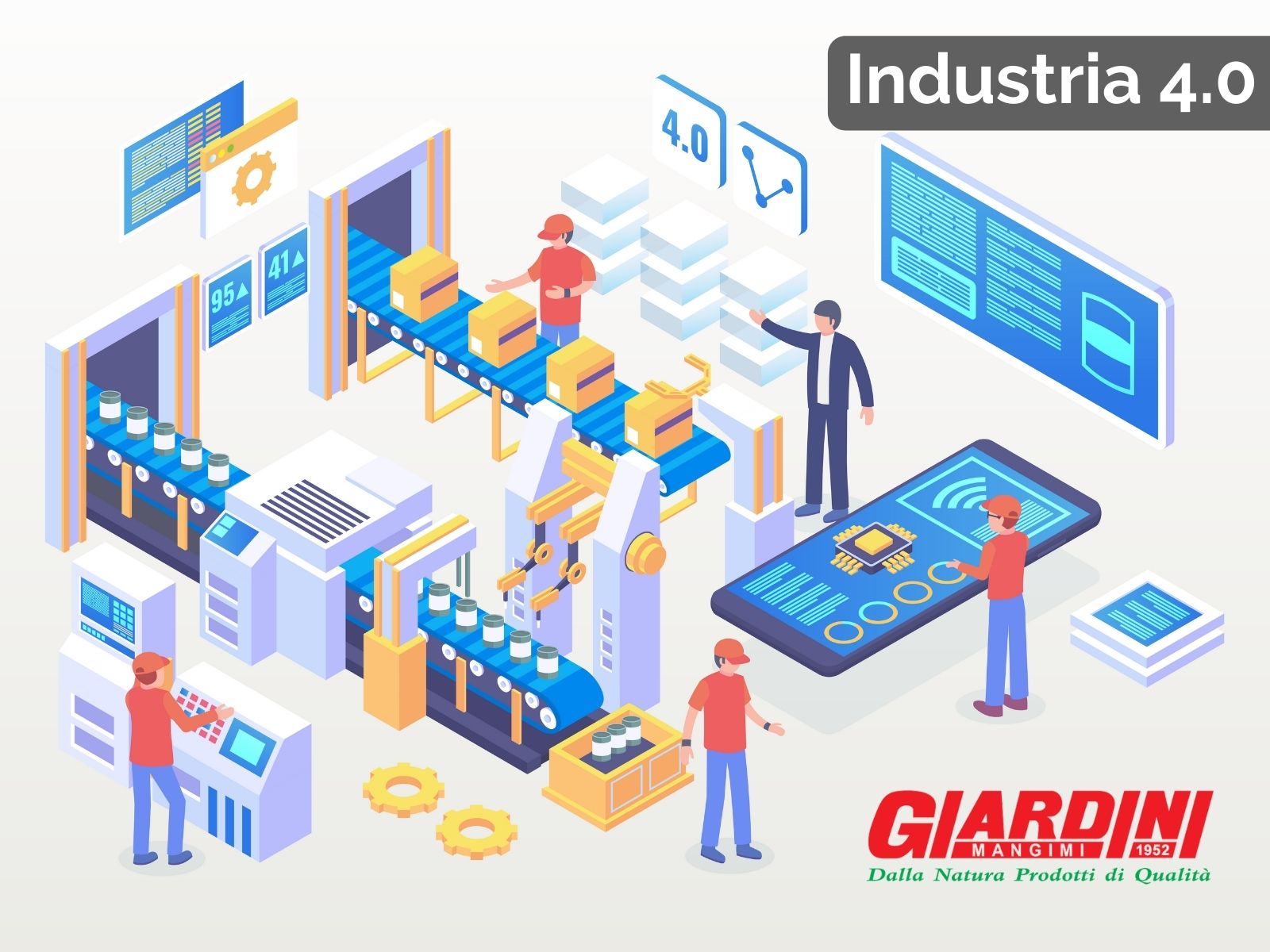
2.Le linee di produzione
A livello di attrezzature ed impianti l’ammodernamento si divide in due parti: la parte relativa agli impianti di produzione definiti “mangimifici” (relativo alla produzione cubettata, in farina e in granaglie), ultimata alla fine del 2017, e la parte relativa all’impianto di “fioccatura” che è stata effettuata nel corso dell’anno 2018.
È però a livello di gestione delle attività e dei processi interni che sono state introdotte delle innovazioni radicali che investono trasversalmente tutta l’organizzazione e la gestione delle funzioni, le attività degli operatori e la gestione del flusso di ogni singolo prodotto: prima tra tutte la piattaforma complessa per la gestione informatizzata integrata di impianti industriali denominata Phoenix. Il sistema permette di gestire la produzione in maniera razionale, semplice e sicura, minimizzando gli interventi degli operatori e le possibilità di errore.
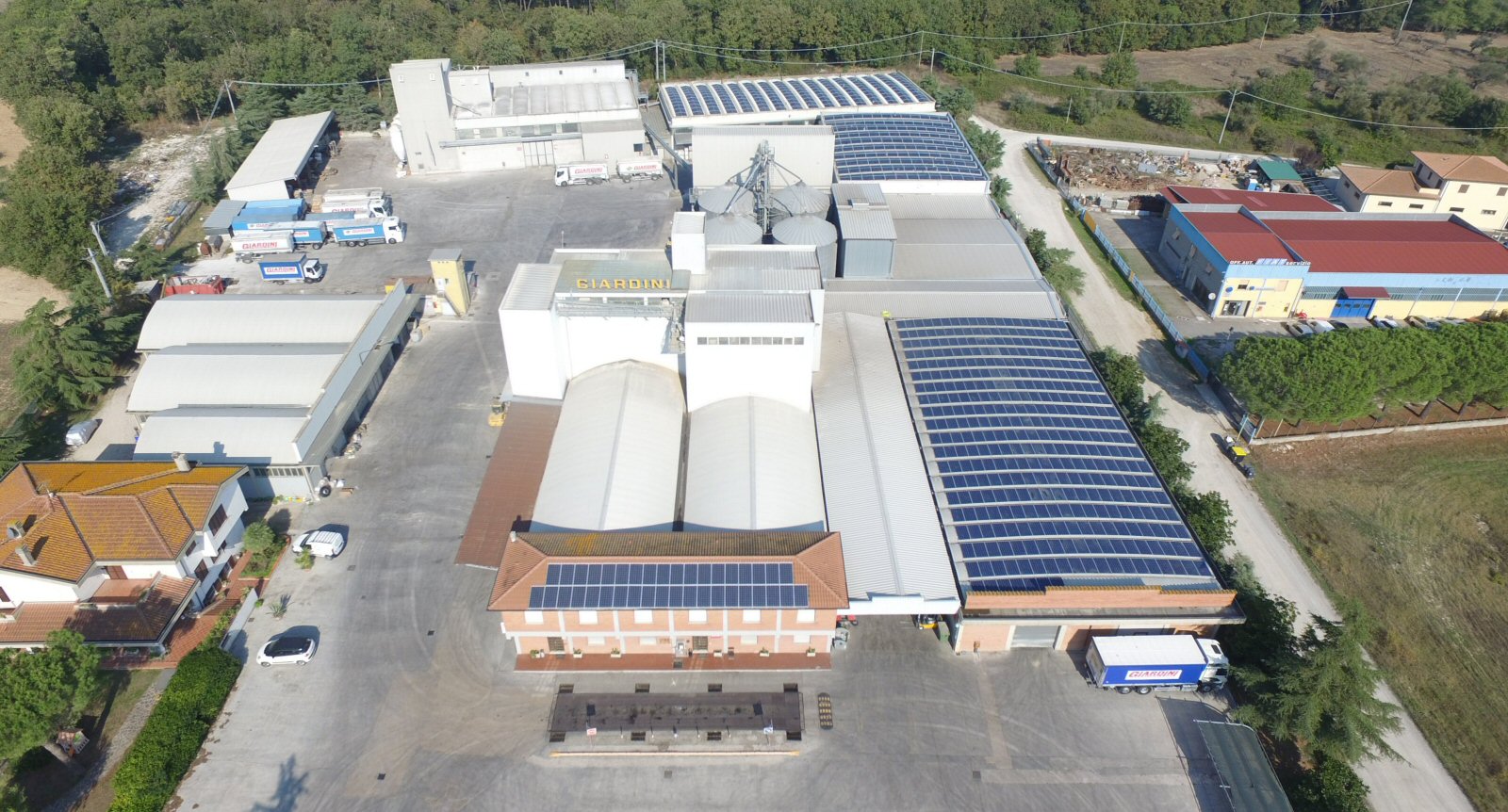
3.Fasi di lavorazione
Tutte le fasi di lavorazione, dall’ingresso materie prime fino all’uscita del prodotto finito, vengono guidate dal sistema in modo da rendere semplici e razionali le operazioni di lavoro, allo scopo di rendere immediatamente efficace e mirato il lavoro del personale e, contemporaneamente, storicizzare le operazioni in modo da consentire una totale tracciabilità della filiera produttiva. L’architettura client/server utilizzata consente di avere più postazioni che operano contemporaneamente sull’impianto e che comunicano tra loro e con le macchine in produzione attraverso la connessione di rete. Il sistema è pensato anche per gestire dei ruoli utente che vengono definiti ed assegnati in fase di installazione e concedono privilegi diversi ai diversi operatori.
Tutte le operazioni ritenute sensibili dal punto di vista della salvaguardia dei dati e della qualità produttiva richiedono l’adeguato livello di accesso da parte dell’operatore, il quale dovrà sempre dare doppia conferma prima di effettuare l’azione la quale, essendo inserita in un flusso continuo “dall’ordine alla produzione alla spedizione”, sarà sempre tracciabile per ogni singolo apparato presente nel sito produttivo.
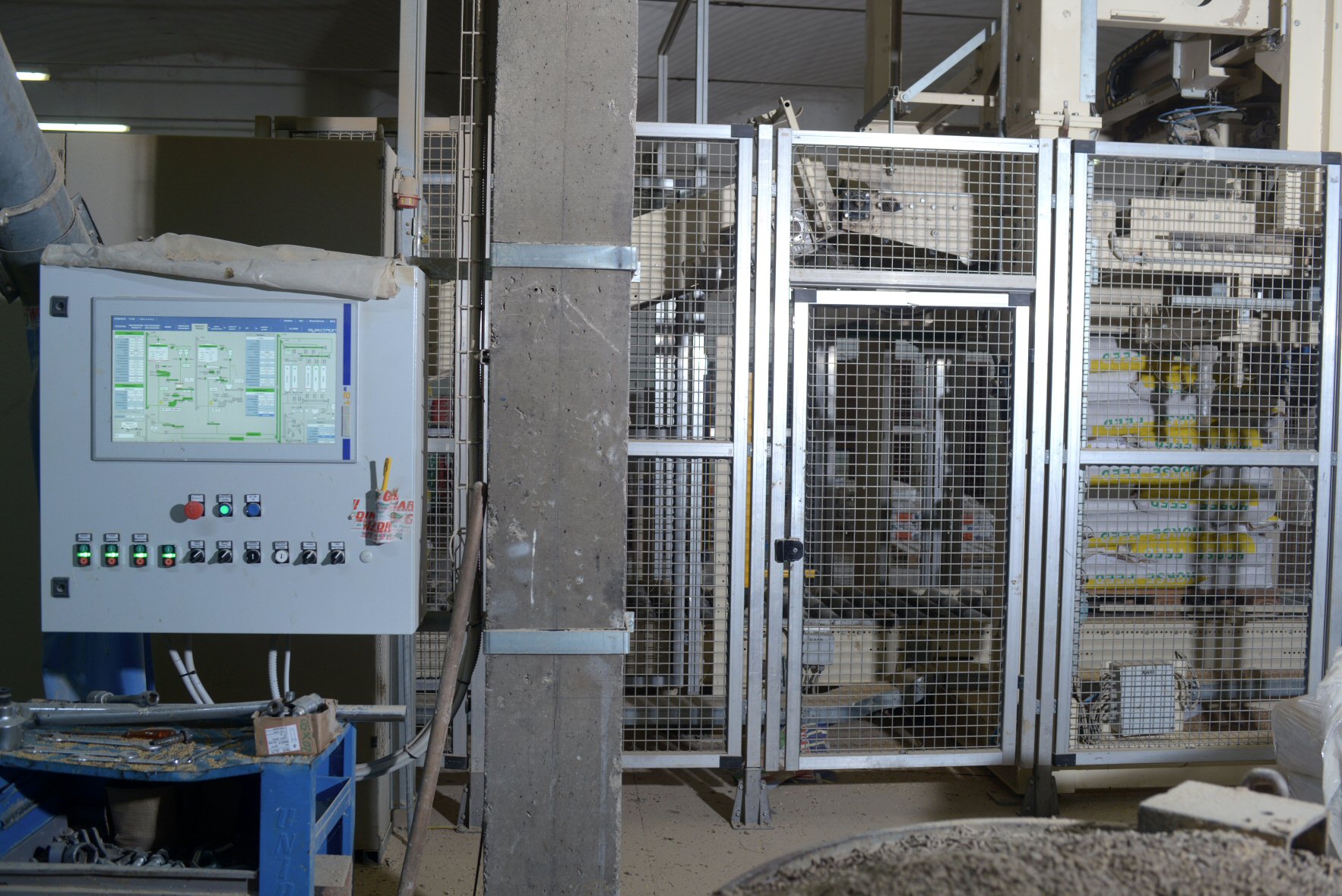
4.Ricezione Ordini
La fase preliminare è quella della ricezione degli ordini di produzione. Gli ordini vengono inviati dalla forza vendita mediante tablet appositamente predisposti, quindi vengono memorizzati nel server (dove risiede il sistema di gestione del PLC di produzione) che li porta a conoscenza dell’operatore di produzione, denominato pianificatore.
Il pianificatore lavora con gli ordini che vengono appositamente smistati per uniformi zone geografiche e per uniformi aree di produzione (per esempio impianto mangimificio, tipo imballaggio, sacchi o rinfusa). Dopo un’attenta verifica il pianificatore manda il flusso di dati verso il sistema di produzione che comanda le macchine nella realizzazione dei prodotti necessari per la vendita. Tale flusso di dati è dinamico e consente un costante adeguamento e adattamento dei flussi di produzione.
5.Ricezione materie prime
La prima fase del ciclo di produzione è quella dell’approvvigionamento delle materie prime utili per tutte le lavorazioni successive in impianto. In tale circostanza l’operatore addetto al carico provvede a raccogliere tutti i dati inerenti la materia prima in arrivo (la qualità, lo stato di conservazione, il lotto del fornitore) e provvede a registrare l’ingresso della materia prima nel sistema. Contemporaneamente potrà indicare la destinazione (o le destinazioni) di stoccaggio ed eventuali operazioni da compiersi durante la fase di scarico/ricezione (es. pulitura, aggiunta additivi, ecc.).
In questa fase di ingresso merci tutte le materie arrivano in azienda legate ad un lotto del fornitore, tutte le materie possono essere movimentate in azienda mantenendo il lotto originale, oppure è possibile assegnare un lotto interno associato a quello del fornitore.
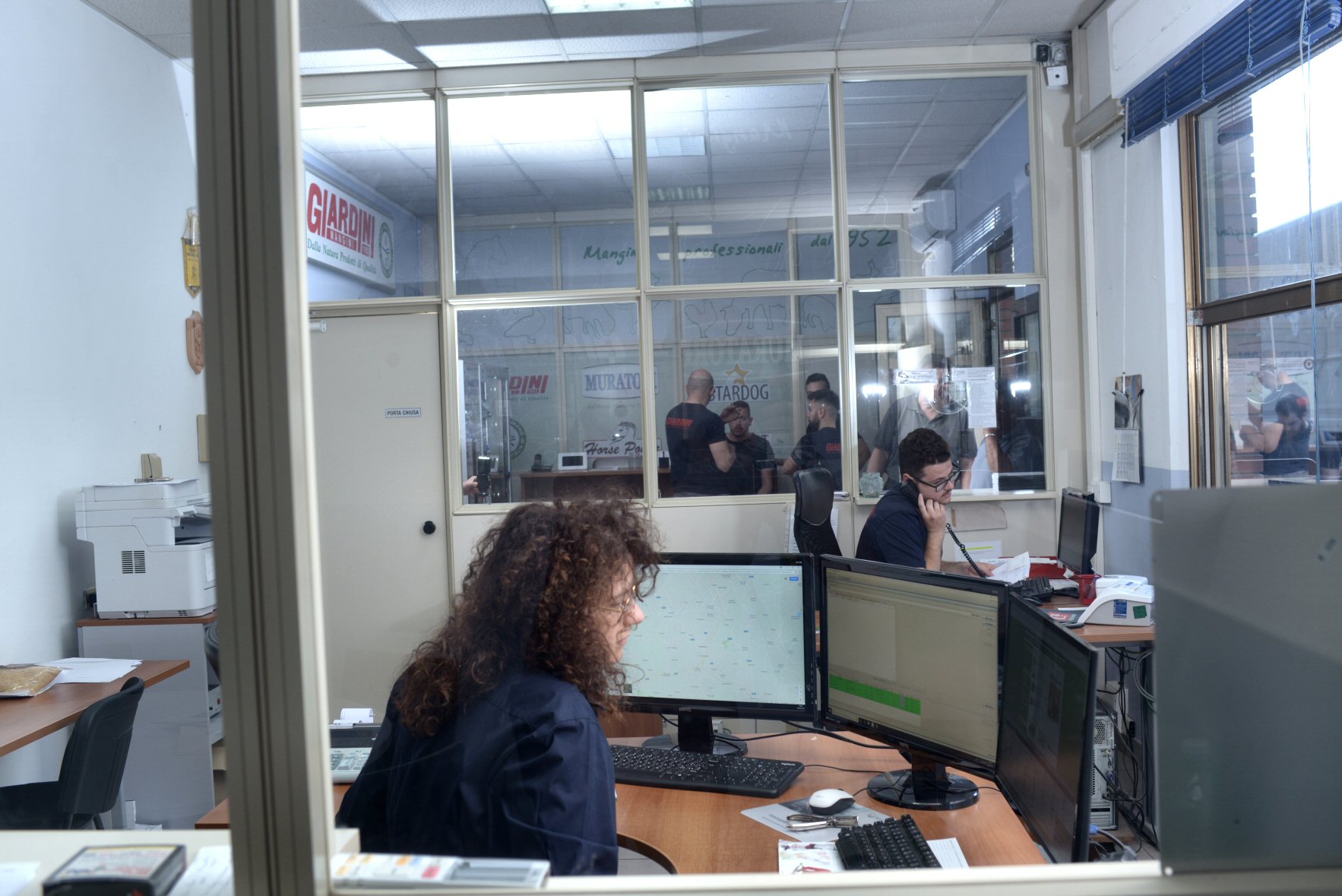
6.Lavorazioni intermedie
Sono la vagliatura, la spezzatura e alcune tipologie di macinatura attraverso le quali l’operatore addetto può impostare diversi parametri guidato nelle possibili impostazioni dal sistema; infatti tutti i dati di lavorazione di un prodotto sono legati al prodotto stesso così come classificato dal sistema.
Il responsabile della qualità (o il formulista) può indicare una serie articolata di parametri per la lavorazione di uno specifico prodotto cosicché l’operatore, quando seleziona quel preciso prodotto dietro originario input del pianificatore, trova già disponibili tutte le impostazioni necessarie, riducendo praticamente a zero le possibilità di errore o la libera interpretazione dell’operatore stesso a garanzia di standardizzazione.
7. Gestione prodotti
La gestione delle anagrafiche prodotti rappresenta un altro punto cardine, infatti ogni materia prima (prodotto) presente nel sistema porta con sé una serie di dati utili a realizzare al meglio tutte le fasi produttive e le lavorazioni presenti in impianto. Tutti questi dati vengono gestiti da personale addetto e preparato, così facendo l’operatore sul campo ha scelte limitate riducendo i possibili errori.
Inoltre si riduce anche la “dipendenza” da operatori esclusivamente preparati o depositari di know-how esclusivi: ogni dipendente, adeguatamente formato, sarà in grado di impostare tutte le operazioni dell’impianto in quanto viene “guidato” passo passo dal sistema stesso che interagisce con i singoli apparati interconnessi. E’ possibile definire per ogni prodotto una o più “tabelle di sostituzione”, ovvero se in fase di formulazione un prodotto non è più disponibile in impianto, potrà essere sostituito da uno o più prodotti simili che ne “replichino” le qualità nutrizionali.
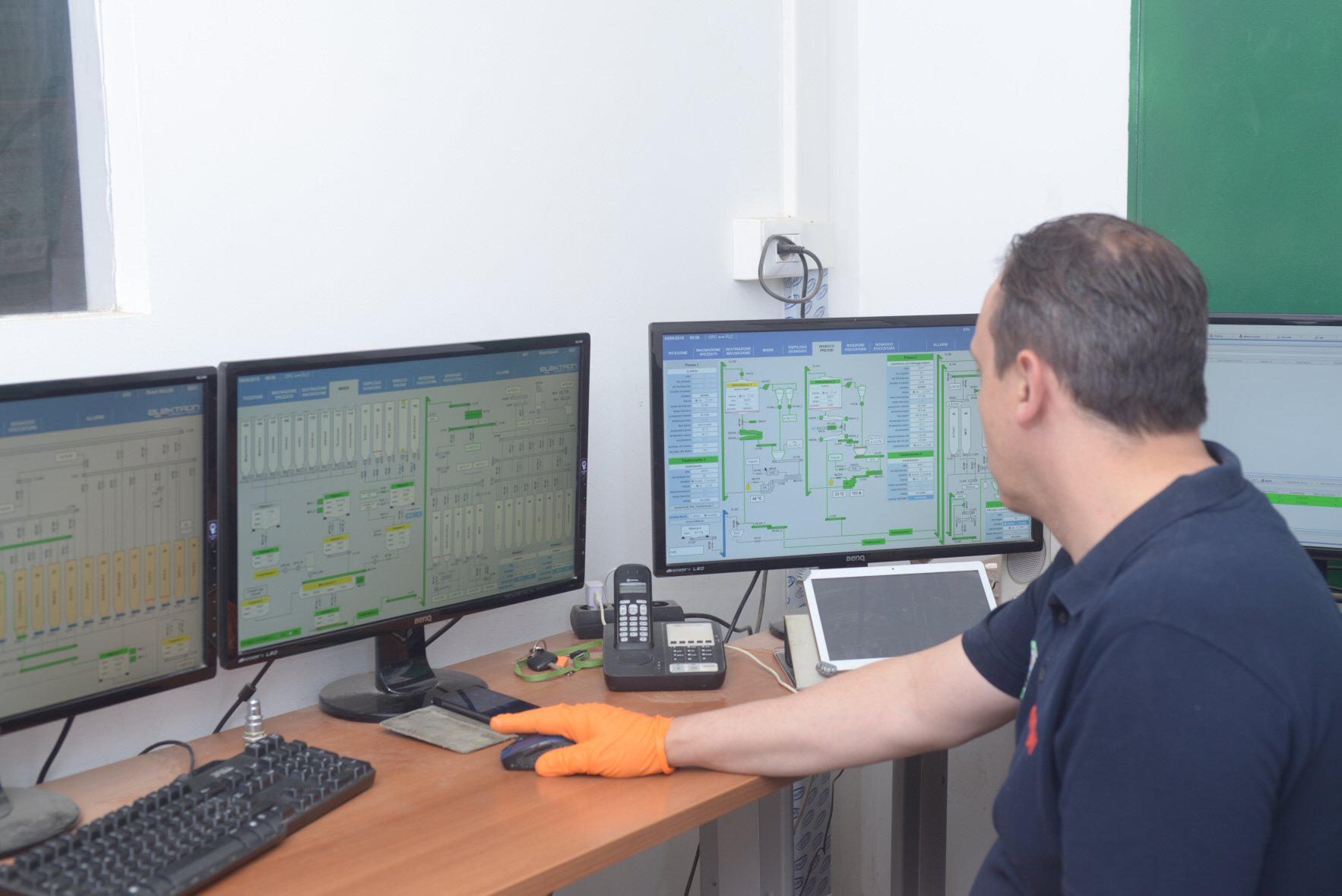
8. Gestione formule
Come per le materie prime (prodotti) anche le formule contengono tutti i dati necessari alla corretta preparazione e realizzazione delle stesse, infatti oltre che contenere tutti i valori (percentuali) necessari per la fase di miscelazione vengono memorizzati anche tutti i dati necessari per le fasi successive (cubettatura detta anche pellettatura, insacco, ecc.).
Per ogni formula è possibile assegnare un gruppo di appartenenza: sempre il responsabile della qualità può definire una serie di compatibilità tra i vari gruppi, andando così a decidere le sequenze di produzione di particolari tipi di mangimi.
Produzione miscele
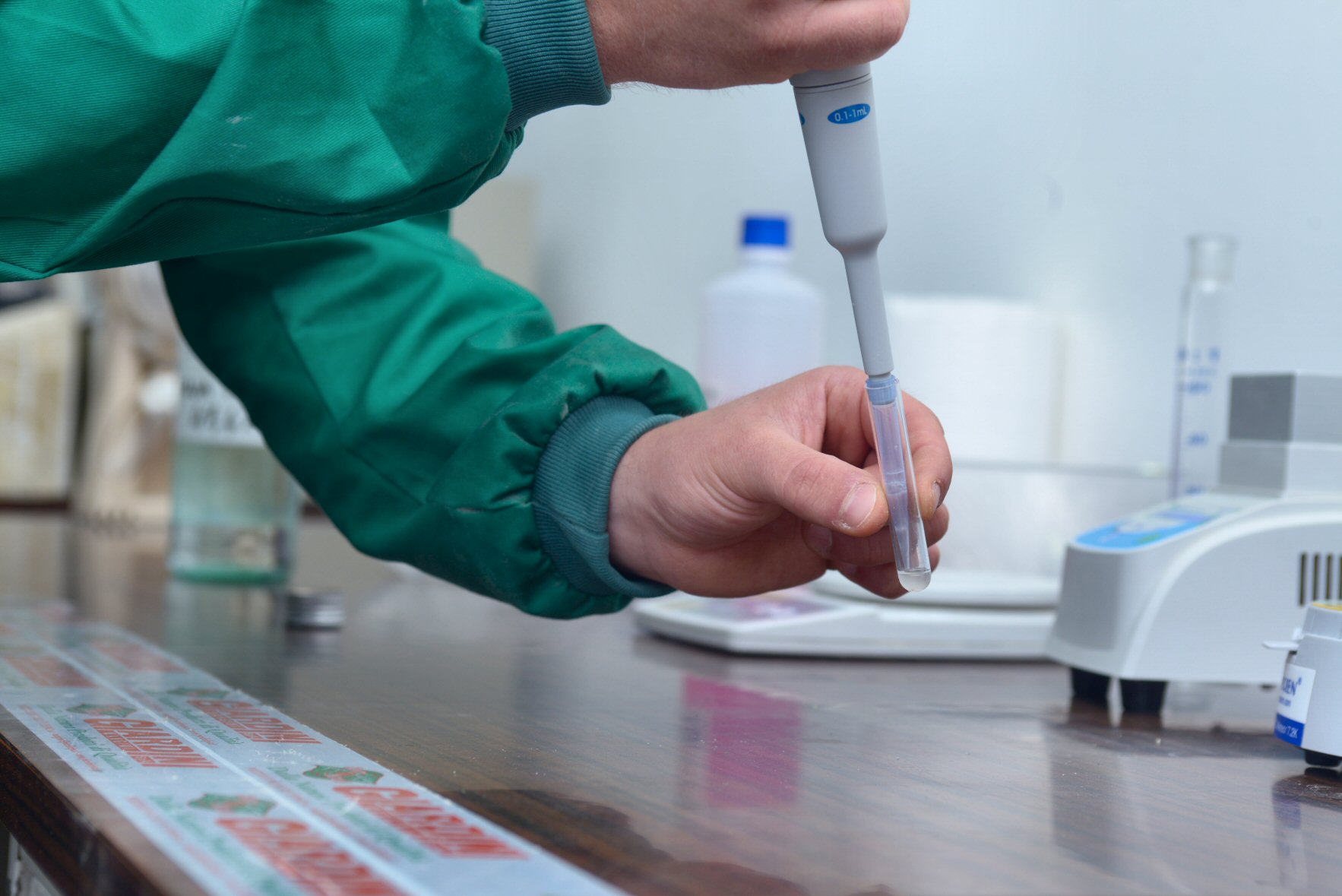
9. Programmazione giornaliera
La fase di produzione segue apposito piano di produzione giornaliero: in base agli ordini o alle esigenze dell’azienda, l’operatore in produzione trova disponibile una tabella di formule da mandare in produzione. Al momento del “lancio in produzione” di una formula il sistema provvede ad effettuare tutti i controlli necessari come: compatibilità con il lancio precedente, disponibilità delle materie prime necessarie alla realizzazione, disponibilità di un silos di destinazione della miscela; in caso di esito positivo si passa alla fase produttiva vera e propria.
Durante le varie operazioni di miscelazione il sistema si occupa di memorizzare tutti i dosaggi effettuati. in questo modo è possibile controllare l’effettivo quantitativo di un prodotto utilizzato attraverso i vari apparati interconnessi e memorizzare il relativo lotto impiegato, così da mantenere i dati per la tracciabilità; registra e segnala eventuali anomalie nel peso del componente (ovvero se viene superata una specifica tolleranza, sia positiva che negativa); richiedere l’aggiunta dei componenti manuali; richiede come agire in caso di mancanza di un componente: sostituirlo con un altro (o una serie di altri componenti) oppure abbandonare la produzione della formula in corso. In ogni momento è possibile monitorare lo stato di avanzamento della produzione e controllare le pesate effettuate da ogni bilancia.
10. Macinazione prodotti
Nel caso in cui la tipologia dei prodotti debba essere macinata prima della fase di miscelazione, il sistema guida il processo di macinazione per integrare le materie necessarie alla produzione delle formule pianificate. Il sistema ottimizza le macinazioni in funzione del consumo del prodotto nelle formule e della sua disponibilità in impianto.
Tutti i dati necessari per la macinazione vengono legati al prodotto stesso, in questo modo il sistema è automatico e l’operatore non deve (e non può) alterare questi stessi dati (ad esempio impostando in maniera errata una macinazione si potrebbe correre il rischio di alterare le proprietà della farina o peggio di danneggiare l’efficienza dell’impianto stesso).
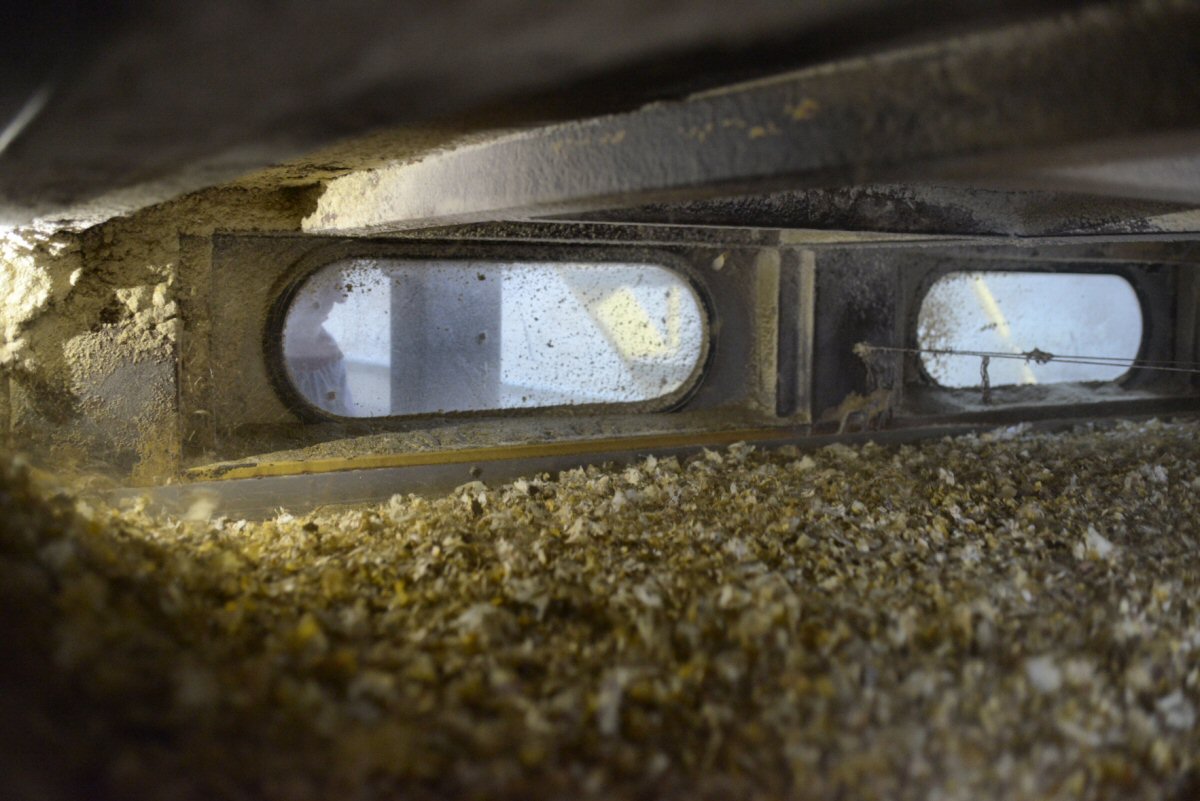
11. Pellet/presse
Anche la fase di pellettatura di un prodotto viene gestita in automatico dal sistema, infatti anche questi dati sono legati al prodotto stesso. L’operatore addetto alle presse deve semplicemente scegliere da quale silo estrarre il prodotto e su quale inviarlo.
La regolazione dei valori della pressa (produzione, temperatura, vapore, ecc.) avviene in automatico grazie al sistema che ottimizza le prestazioni e riduce l’interazione con l’operatore.
12. Fasi finali (insacco/rinfusa)
Durante queste fasi potrebbe essere necessario completare la produzione della formula aggiungendo ad esempio dei prodotti fioccati o additivi di conservazione (o tutti quei prodotti non utilizzabili in fase di miscelazione), il sistema provvede ad aggiungere le parti mancanti e guida l’operatore consentendo solo le operazioni specifiche per quella tipologia di mangime; ad esempio a livello di formula è possibile indicare che tipo di insacco può essere scelto (sacco da 10 kg o da 25 kg o altro ancora) impedendo così la scelta di un eventuale formato non previsto commercialmente o che gli apparati confezionerebbero in maniera errata.
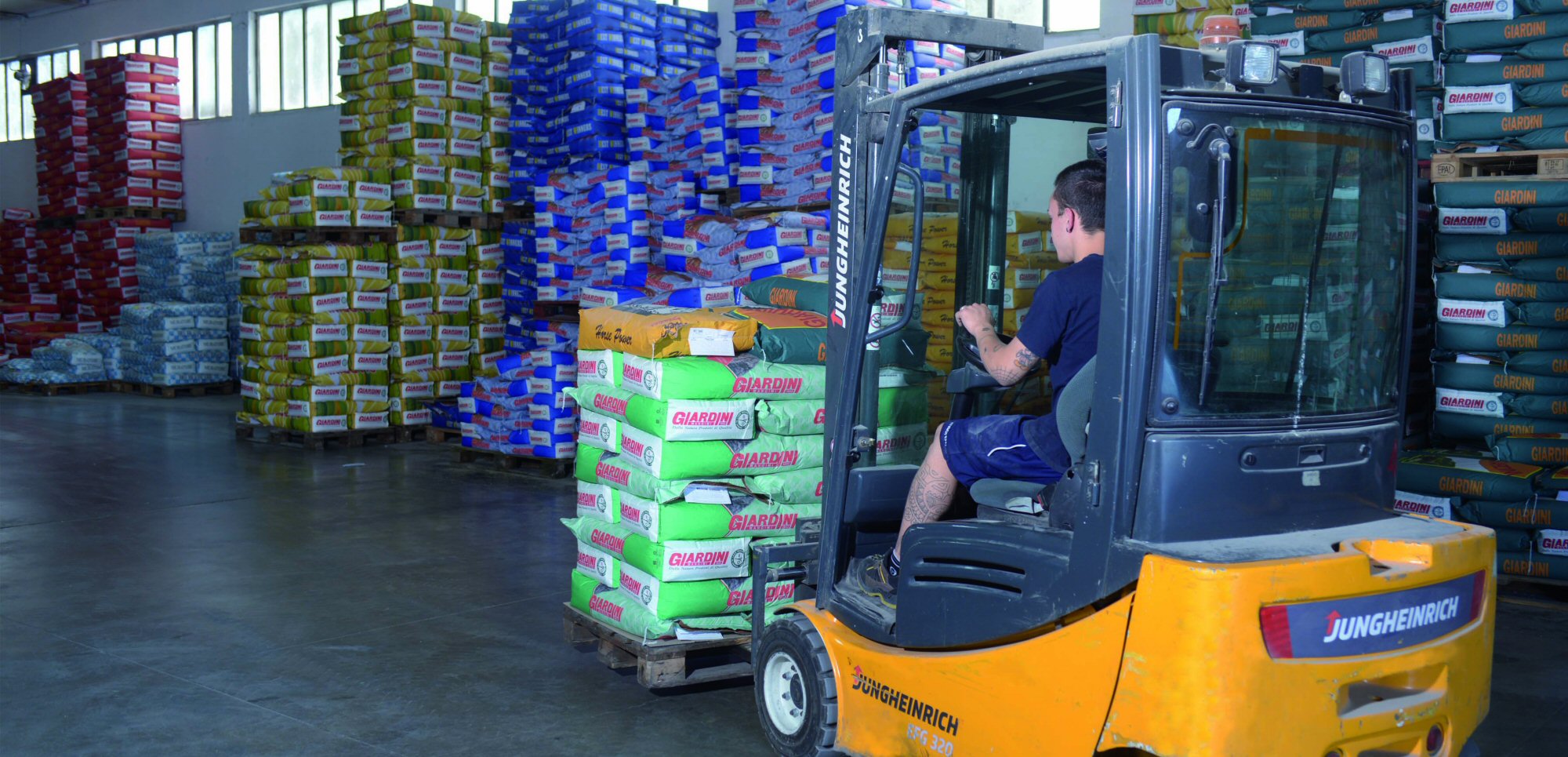
13. Programmazione e spedizione
Una volta realizzato il prodotto in sacchi o rinfusa il sistema rimanda i flussi all’addetto alla produzione chiamato pianificatore il quale verifica la possibilità di caricare i vari automezzi come da programma iniziale, ne prevede la spedizione, ne controlla la rintracciabilità e la campionatura ai sensi di legge. Inoltre scarica i dati dal sistema di produzione liberando le risorse per le produzioni dei giorni successivi.
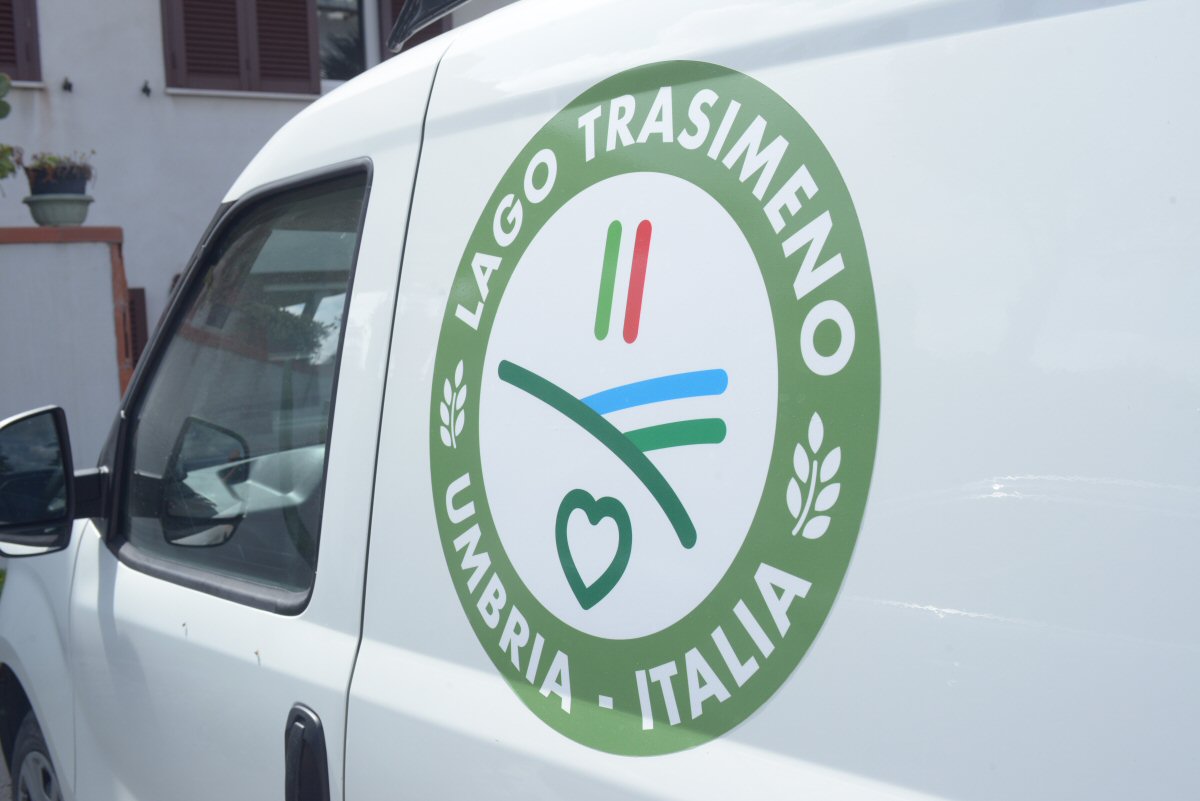
14. Struttura informatica
Il sistema di gestione dell’impianto di produzione mangimificio è stato strutturato in modalità client-server, in pratica tutto l’impianto viene gestito da un server e tutte le postazioni degli operatori sono dei semplici client che si collegano direttamente al server dove risiede l’intelligenza che guida ogni apparato. È possibile in ogni momento aggiungere nuovi server per aumentare la sicurezza del sistema. Tutte le informazioni elaborate e/o gestite dal sistema sono facilmente consultabili da parte dell’operatore tramite opportuni report, all’occorrenza anche visibili su altre piattaforme/tecnologie web.
15. Sistema di gestione
Il sistema di gestione del processo produttivo della Giardini spa è stato denominato Phoenix Giardini ed è così composto:
Phoenix PLC Giardini: è il cuore dell’impianto, si occupa dell’interfacciamento con il campo, controlla i sensori, gli attuatori, le motorizzazioni e riporta lo stato dell’impianto al server e, attraverso il server, ai vari client.
Phoenix Server Giardini: è la mente dell’impianto, poiché è l’unico a comunicare effettivamente con Phoenix PLC Giardini, assegnandogli i comandi da eseguire e andando a leggere lo stato dell’arte. Phoenix Server Giardini, inoltre, è il cuore dell’applicativo, su di esso vengono memorizzati tutti i dati di archiviazione quali le anagrafiche delle formule, le materie prime, i report di produzione e tutti gli altri dati riguardanti la produzione.
Phoenix Client Giardini: permette la gestione vera e propria dell’impianto come descritta di seguito quindi: la gestione dell’archivio delle formule, la gestione dell’archivio delle materie prime, la ricerca di report di produzione, dosaggio, ricezione, riciclo, l’avvio di operazioni di dosaggio (ricezione, riciclo, ecc.).
Phoenix Supervisor Giardini: si esemplifica nell’interfaccia utente, poiché mostra lo stato dell’impianto: da questo si possono supervisionare e visionare non solo tutti i macchinari e relativi apparati connessi, ma, grazie ad animazioni (colorazioni di flussi ad esempio verdi o rossi o grigi ecc..), se ne può dedurre lo stato degli stessi, ovvero se sono attivi o meno. Dalla postazione del supervisore, inoltre, si possono effettuare piccole correzioni di alcuni parametri di lavoro durante le varie operazioni del macchinario stesso. La postazione del supervisore permette anche, tramite appositi pulsanti, di aprire maschere di gestione del Phoenix Client Giardini.
16. Caratteristiche tecniche
Da un punto di vista strettamente tecnico come detto il progetto di rinnovo degli impianti ha previsto in primis l’aggiornamento completo hardware e software del plc e della piattaforma di supervisione. Per l’automatizzazione dei reparti sono stati utilizzati un plc Omron e un plc Allen-Bradley. Entrambi i plc comunicano mediante OPC server con il software gestionale Phoenix (opportunamente sviluppato e personalizzato) e con lo scada. Come scada è stata implementata la piattaforma Wonderware System Platform. Leader mondiale nelle soluzioni per l’automazione, Wonderware by Schneider Electric mette a disposizione una piattaforma complessa ma dinamica e customizzabile, sulla quale i tecnici hanno lavorato vari mesi per metterla a punto secondo le esigenze del cliente, con l’obiettivo di renderla quanto più efficiente e semplice da utilizzare possibile. Il revamping ha previsto un avanzamento dell’attività a step, coinvolgendo inizialmente gli apparati ricezione e trasferimenti, per proseguire successivamente con i reparti macinazione, rinfusa e insaccamento.
Il suddetto sistema permette di gestire la produzione in maniera semplice e sicura, minimizzando gli interventi degli operatori e, dunque, i possibili errori. Grazie ad una progettazione modulare, il sistema può crescere insieme all’impianto stesso, consentendo una facile integrazione con strumenti esistenti o futuri. Come detto tutte le fasi di lavorazione, dall’ingresso materie prime fino all’evasione del prodotto finito, vengono gestite e guidate dal sistema con operazioni di lavoro semplici ed intuitive per l’utente; nel contempo il sistema provvede a storicizzare le operazioni per consentire una totale tracciabilità della filiera produttiva. L’architettura client/server utilizzata consente di avere più postazioni che operano contemporaneamente sull’impianto e che comunicano tra loro attraverso la connessione di rete; il sistema è pensato anche per gestire dei ruoli utente che vengono definiti ed assegnati in fase di installazione e concedono privilegi diversi ai diversi operatori.
Considerazioni strategiche
La strategia di base è stata quella di creare una condivisione di dati ed informazioni gestite da un sistema intercomunicante e connesso, integrato tra impianti, silos materie prime, pianificazione, gestione e controllo della produzione, magazzino e spedizioni, nonché amministrazione, acquisti e commerciale, perfettamente in linea con lo spirito di Industria 4.0.
La realizzazione del piano formativo qui descritto è stata parte integrante e necessaria del piano di ammodernamento tecnico e riorganizzazione sopra descritto: grazie alla sua attuazione ogni operatore ha acquisito le conoscenze e le competenze necessarie ad utilizzare al meglio tutto il sistema integrato, il corretto funzionamento del quale apporta consistenti benefici nella razionalizzazione di tutto il processo, un incremento della produttività degli impianti e della qualità del prodotto, nonché un ampliamento della motivazione e delle competenze professionali di tutti i dipendenti, anche nell’ambito di ruoli operativi nuovi, della promozione della prevenzione e protezione, e del miglioramento delle condizioni di lavoro in generale.
Investimenti Produttivi Finanziati
Tra il 2016 e il 2017 abbiamo presentato una richiesta di contributo per gli investimenti poi effettivamente realizzati negli anni successivi a valere per l’Intervento 4.2.1 “Sostegno agli investimenti per la trasformazione, commercializzazione e/o lo sviluppo di prodotti agricoli” del Programma di Sviluppo Rurale per l’Umbria 2014/2020 (PSR) approvato dalla Commissione UE con decisione n. C(2015)4156 del 12 giugno 2015 e finanziato con i fondi comunitari FEASR.
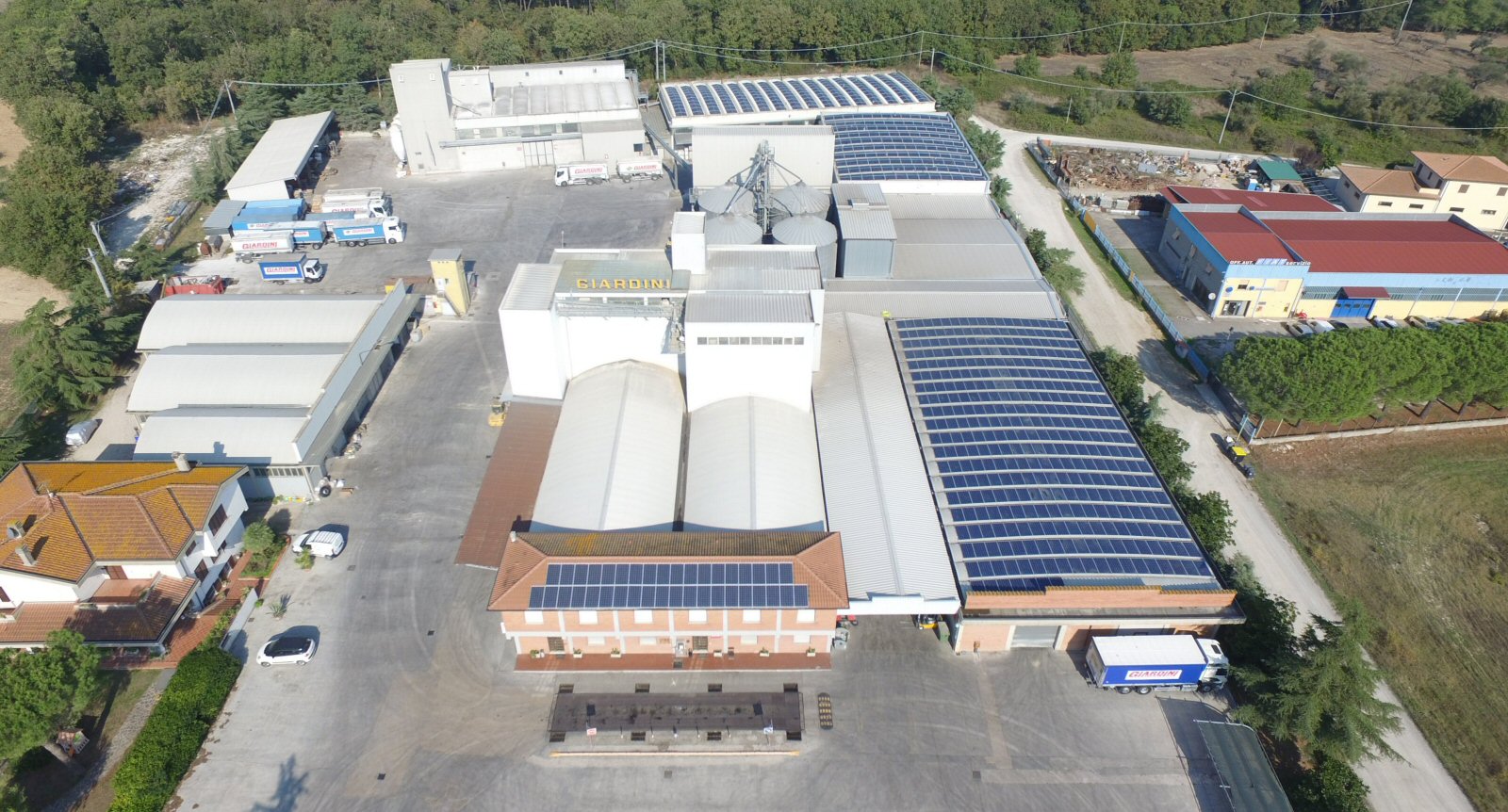